Фахівці Інституту чорної металургії розробили технологію, що дає змогу під час виплавки значно зменшити витрати коксу і природного газу
«Голос України» уже не раз писав про одну з найгостріших проблем вітчизняної металургії — відсутність необхідної кількості якісного коксу для доменної плавки. Як шлях розв’язання цієї проблеми, часто пропонується просто возити кокс із далекого зарубіжжя. Проте є й більш економічно вигідна для нашої держави альтернатива, розроблена українськими вченими і виробничниками.
Гаряча альтернатива
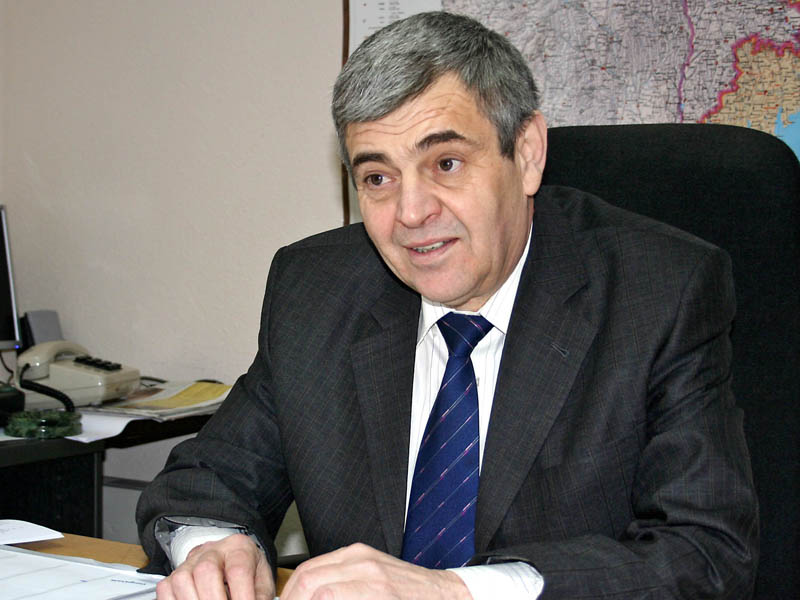
— Попри це, ви все-таки обстоюєте впровадження в металургії України технології вдування пиловугільного палива?
— Така технологія вже пройшла «обкатку» на передових металургійних підприємствах світу. Але цьому передувало докорінне поліпшення якості залізорудної сировини і коксу, вдосконалення параметрів режиму доменної плавки та керування процесами в печі. Ці підприємства працюють з витратами коксу лише 300—350 кілограмів на тонну виплавленого чавуна при вдуванні 150—200 кілограмів пиловугільного палива — економія чимала. Щоправда, вагомих показників досягнуто за рахунок використання залізорудної сировини з високим вмістом заліза, а також застосування якісного і міцного коксу.
Нині металургія України не має сировини і коксу такої якості. Природно, виникнуть проблеми з освоєнням технології вдування в доменні печі пиловугільного палива до економічно виправданого рівня 150—200 кілограм на тонну виплавленого чавуна. Приміром, для доменної печі №2 металургійного заводу «Донецьксталь», на якій удувають до 145 кілограм пиловугільного палива на тонну чавуна, довелося організувати постачання спеціального коксу «Преміум» високої якості.
Ефективно, тільки дорого
— Отже, технологія вдування економічно вигідна, тільки впровадити її в наших умовах неможливо. Адже знову все впирається в якісний кокс, якого в нас немає.
— Справді, впровадженню будь-якої нової технології передує розробка техніко-економічного обґрунтування. Будівництво сучасної агломераційної фабрики, що може забезпечити доменне виробництво агломератом з низьким вмістом дрібних фракцій і високим вмістом заліза, потребує інвестицій на рівні від 500 мільйонів до мільярда доларів. Будівництво інфраструктури в глибоководному морському порту для доставки якісного коксівного вугілля з далекого зарубіжжя (його все одно доведеться імпортувати, хоча й не в таких кількостях) — це ще 100—200 мільйонів доларів. Для організації удування пиловугільного палива необхідно спорудити на кожен доменний цех капіталомісткий комплекс вартістю 45—70 мільйонів доларів, що включає, зокрема, устаткування для одержання, транспортування і дозування пиловугільного палива перед подачею в доменну піч. До того ж запаси пісного і газового вугілля в Україні обмежені, і при широкому впровадженні технології вдування їх також доведеться імпортувати з близького чи далекого зарубіжжя.
Незважаючи на перелічені проблеми, нині альтернативи повсюдному впровадженню такої технології, що значно знижує витрати коксу, в доменній плавці немає. Питання тільки у вартості та часі.
Перехідний період: можна обійтися без величезних капітальних витрат
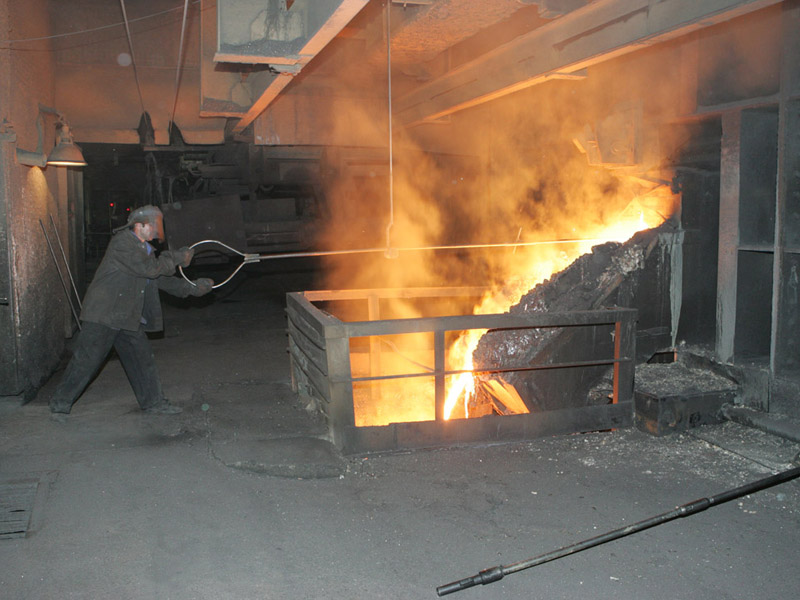
— Саме тому українськими вченими і виробничниками розроблено низку інших випробуваних у виробництві й перспективних технологій заміни коксу у доменній плавці, що дають трохи менший економічний ефект, аніж пиловугільне паливо, але не потребують великих капітальних витрат, а також часу на їх впровадження. В умовах різкого подорожчання природного газу, дефіциту коксу, нестачі інвестицій і тривалих термінів упровадження технології пиловугільного палива мають право на здійснення також технології, розраховані на перехідний період. У цьому зв’язку особливого значення набуває технологія заміщення коксу кусковим вугіллям. Вона докладно викладена в праці «Розробка і впровадження комплексу технологій зниження витрат коксу і природного газу для підвищення ефективності виплавки чавуна і феросплавів» і висунута Інститутом чорної металургії ім. З. І. Некрасова НАН України на здобуття Державної премії України в галузі науки і техніки за 2009 рік.
Оскільки кускове вугілля відрізняється від коксу за фізико-механічним і термохімічним властивостям, їх завантажують за особливими програмами (технологія запатентована в Україні й Росії). На сьогодні така технологія завантаження в доменні печі великого обсягу сирого кускового антрациту в кількості 70—80 кілограм на тонну чавуна апробована у вигляді тривалих експериментів на комбінаті «Криворіжсталь» (нині —ВАТ «АрселорМіттал Кривий Ріг»). Особливо треба відзначити досвід роботи найбільшої доменної печі України обсягом 5000 кубічних метрів на технології з частковою заміною коксу кусковим антрацитом до 90 кілограм на тонну чавуна. Капітальні витрати на реалізацію цієї технології практично відсутні, а ефективність визначається співвідношенням властивостей вугілля та його ціни і дозволяє мати економію від 2,1 до 17,5 долара на кожній тонні виплавленого чавуна.
Використання сирого антрациту, термоантрациту і термобрикетів для часткової заміни коксу дає змогу оперативно розв’язати низку проблем доменного виробництва до освоєння технології вдування пиловугільного палива.
У результаті впровадження цих наукових розробок уже отримано економічний ефект на трьох підприємствах галузі: «Криворіжсталі», Нікопольському заводі феросплавів і Запорізькому феросплавному заводі — понад 470 мільйонів гривень. А поширення на всю галузь дозволить одержувати щорічно економічний ефект до мільярда гривень.
Інтерв’ю взяла Галина КВІТКА.
На знімку: на Нікопольському заводі феросплавів.
Фото Олександра КЛИМЕНКА (з архіву «Голосу України»).