Але заощаджувати газ на їхньому виробництві можна
Тема енергозбереження є однією з основних у питанні забезпечення національної безпеки України. Тільки навчившись ощадливо витрачати непоправні ресурси, ми можемо розраховувати на сталий розвиток економіки. А, отже, і добробут громадян. Тому розробка і впровадження проектів у цьому напрямі повинні мати найвищий пріоритет у державній політиці.
Саме цій темі присвячено роботу вчених Національної металургійної академії України в співавторстві з ПАТ «Нікопольський завод феросплавів» і Державним підприємством «Український науково-технічний центр металургійної промисловості «Енергосталь» — «Новітні енергозберігаючі технології виробництва марганцевих феросплавів в електропечах».
Випуск сталі у світі постійно зростає, і нині становить майже 1,6 млрд. тонн на рік. Відтак підвищується й потреба сталеплавильної промисловості в марганці та інших феросплавах. У 2013 році виробництво марганцевих феросплавів в Україні становило 710 тис. тонн, зокрема, 429 тис. тонн виготовлено на одному з найбільших світових виробників — ПАТ «Нікопольський завод феросплавів».
Виробництво феросплавів пов’язане зі значним енергоспоживанням. Досить сказати, що потужність споживачів електроенергії НЗФ становить 1366 МВА, що відповідає 10% виробництва Дніпровської електроенергетичної системи, або 2,5% споживаної електричної енергії всієї України. Значним було й споживання природного газу.
Мінус мільйони кубометрів
Незважаючи на досягнуті високі показники у виробництві марганцевих феросплавів, перед НЗФ cтоїть низка проблемних науково-технологічних і екологічних завдань, які можуть бути успішно вирішені під час проведення системних теоретичних, експериментальних досліджень і дослідно-промислових робіт із широким впровадженням результатів у виробництво.
— Ученим і виробничникам удалося створити й впровадити новітню технологію виробництва марганцевих феросплавів, — розповів «Голосу України» один з розробників, генеральний директор НЗФ Володимир Куцин (на знімку). — Так, впровадження технології запалювання шихти на агломашинах ферогазом, який попутно утворюється в електропечах під час виробництва феросплавів і раніше просто спалювався на свічах через свою відносно низьку калорійність, забезпечило за період використання економію 83 мільйони кубометрів природного газу. Істотна частина дорогого й дефіцитного коксика дрібних фракцій заміщена антрацитом: економія коксу становить понад 82 тис. тонн.
Вдалося вирішити питання й зниження електроспоживання. Впроваджена система для розрахунків раціональних електричних режимів виплавки феросилікомарганцю і феромарганцю забезпечила зниження питомої витрати електроенергії, підвищення продуктивності печей і стабільну роботу устаткування в умовах зонної тарифікації електроенергії.
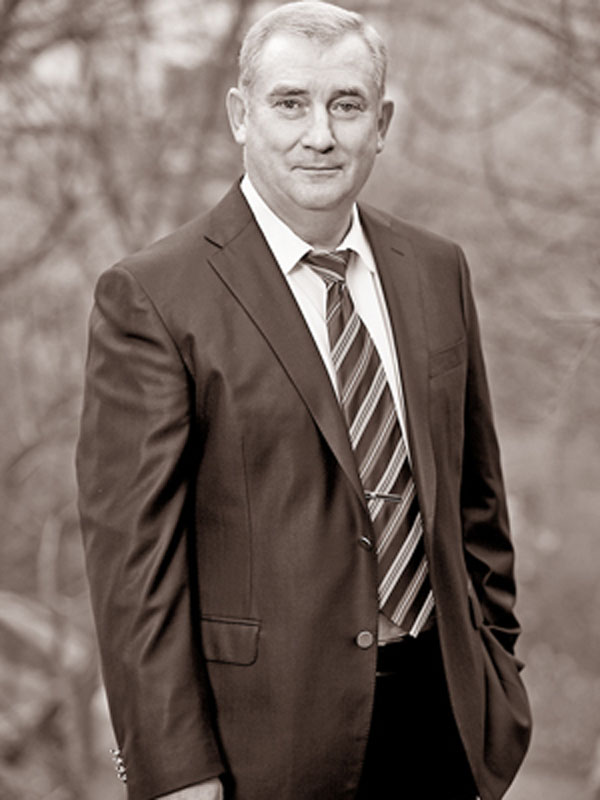
— Створено теоретичну основу моделювання розподілу електричної потужності у ваннах феросплавних електропечей різної конструкції, — зазначив професор Донбаської державної машинобудівної академії Олександр Тарасов. — Створена інформаційна технологія управління електропечами дозволила підвищити продуктивність електропечей з одночасним зниженням витрат на електроенергію.
На основі сучасних ІТ-технологій були розроблені й досліджені математичні моделі, створено новітню технологію виплавки феросилікомарганцю з використанням марганцевого магнезіального агломерату. Усе це дало змогу одержувати оптимальний склад шлаку для зниження питомої витрати сировинних матеріалів.
— Комп’ютерна реалізація методів аналізу дає можливість приймати критичні рішення на початкових стадіях планування й проектування технологічних процесів у металургії, — коментує професор Харківського національного університету Григорій Жолткевич. — Це є одним з вирішальних чинників одержання економічного ефекту.
Використання вторинних ресурсів виходить на перший план
Неабияку увагу вчені приділили й питанням екології. Так, було розроблено систему моніторингу процесу поширення пилогазових викидів при виробництві феросплавів, впроваджено інноваційне обладнання для сухого очищення пилогазових утворень для мінімізації впливу на довкілля. Модернізовані системи сухого очищення аспіраційних пилогазоповітряних викидів. За отриманими у роботі вихідними даними на заводі було побудовано ще одну газоаспіраційну станцію потужністю 500 тисяч кубометрів на годину з рукавними фільтрами, що дало змогу знизити викиди забруднюючих речовин в атмосферу менш припустимої концентрації.
Економічний ефект НЗФ від впровадження розробок лише торік становив понад 330 мільйонів гривень. За весь період цифра перевищила 2,5 мільярда.
— Значним внеском у роботу є розробка екологічного напрямку, використання вторинних ресурсів, — зазначають у ПАТ «ММК імені Ілліча». — Це цілком відповідає завданням відповідних регіональних і державних програм.
Зниження вартості продукції НЗФ, яке стало можливим завдяки впровадженню цих розробок, гідно оцінили вітчизняні споживачі. Та й на міжнародному ринку конкурентоспроможність продукції Нікопольського заводу значно зросла завдяки більш низьким витратам споживачів на виплавку сталі.
— Завод постійно займається зниженням вартості виробленої продукції, впровадженням прогресивних і енергозберігаючих технологій, — розповів комерційний директор ПАТ «МК «Азовсталь» Євген Поскачей. — Як споживачі такої продукції, ми завжди звертаємо на це особливу увагу.
Реформування поставили на наукову основу
Головним підсумком стало розв’язання актуальної й пріоритетної науково-технологічної проблеми ГМК відповідно до Держпрограми розвитку й реформування галузі. Це підвищення виробництва конкурентоспроможних марганцевих феросплавів у потужних електропечах на основі розробки й впровадження науково-обґрунтованих інноваційних технологій і устаткування.
Основні результати роботи опубліковані в дев’ятьох монографіях, 76 статтях у спеціалізованих наукових журналах, 26 статтях у збірниках наукових праць і доповідей наукових конференцій. Новизна технічних рішень захищена 29 патентами. За цією роботою захищено дві докторські й чотири кандидатські дисертації. Своєю головною заслугою розроблювачі вважають внесок в енергонезалежність України й забезпечення стабільного розвитку вітчизняної економіки.
Провідні вчені й виробничники вважають, що робота «Новітні енергозберігаючі технології виробництва марганцевих феросплавів в електропечах» та її творчий колектив заслуговують на присудження Державної премії України в галузі науки й техніки 2014 року.
Дніпропетровська область.
Дослівно
— Необхідно відзначити оригінальність пропонованих рішень, що дозволяють мінімізувати антропогенний вплив на довкілля процесів виплавки феросилікомарганцю, — вважає директор Карагандинського хіміко-металургійного інституту (Казахстан) Манат Толімбеков. — А також заміну дорогого природного газу на ферогаз.
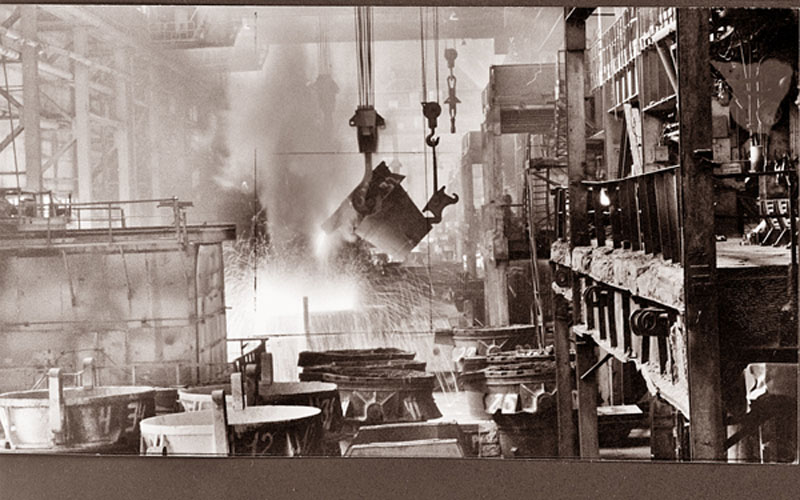
Фото з архіву Нікопольського заводу феросплавів.